New energy, also known as unconventional energy, refers to various energy forms other than traditional energy sources, such as solar energy, geothermal energy, wind energy, ocean energy, biomass energy and nuclear fusion energy. At present, China's new energy utilization technology has made considerable progress and has formed a certain scale in various regions, especially in the wind energy field. Recently, the country has introduced a new energy development plan. Wind power, as a key supporting industry, has a broader development prospect.
Wind Energy Overview Compared with other types of new energy sources, the unique advantages of wind energy make it attractive for new energy development and utilization.
First, the reserves are large and widely distributed. China's proved theoretical wind energy reserves are 32.26×109 kW, while 2.53×109 kW can be exploited and utilized, and 7.5×109 kW of wind energy can be used offshore. The southeast coast of China and Inner Mongolia, Xinjiang, Gansu and other northeast and northwest regions are the largest areas of wind energy resources.
Second, the availability is strong and the cost is relatively low. At present, the cost of wind farms is about 8500 to 9,000 yuan/kWh, with units (equipment) accounting for about 70%, infrastructure 25%, and others 5%. Wind farm operation and maintenance costs are very low (about 3% to 5% of wind turbine components), and the construction period is short (about half a year). Once built, wind farms are an endless source of money.
Wind power technology core wind power system as a core part of the wind power generation field, technological progress is also changing. At present, there are two major categories of constant-speed constant-frequency wind generator systems and variable-speed constant-frequency wind generator systems.
Constant-speed constant-frequency wind power generation systems generally use synchronous motors or squirrel-cage asynchronous motors, and the rotational speed of the generator is maintained at a constant value through a wind turbine with a fixed pitch stall to ensure the frequency and amplitude of the generator-side output voltage. It is constant, its operating range is relatively narrow, and it can only capture wind energy at a certain wind speed, and its power generation efficiency is low.
Variable-speed constant-frequency wind power systems generally use permanent-magnet synchronous motors or doubly-fed motors as generators. By pitch-controlling the wind turbines, the entire system can be operated with the highest efficiency in a wide range of speeds. This is the current wind power technology. The direction of development. For wind turbines, the speed range is generally between 50% and 150% of the synchronous speed. If an ordinary squirrel cage induction motor system or a permanent magnet synchronous motor system is used, the capacity requirements of the inverter and the capacity of the generator being dragged Quite, very uneconomical. The stator of a doubly-fed asynchronous wind power generation system is directly connected to the power grid. The rotor and the power converter are connected. The power passing through the converter is only the differential power. This is a relatively high efficiency in various transmission systems. The structure is suitable for speed regulation. A wide range of wind power systems, especially large and medium-sized wind power systems.
The use of a wound induction motor as a generator and control of its rotor current is one of the main forms of realization of a variable-speed constant-frequency asynchronous wind power generation system. The main topology includes AC excitation control, rotor chopping resistance, and a hybrid structure developed from the combination of the two topologies.
1 AC excitation structure Excitation control The frequency converter provides three-phase slip frequency current to the rotor for excitation. Frequency converters in this method usually use cross-converters, matrix converters, or AC-DC converters.
2 The basic idea of ​​this structure is to use a controllable power electronic switch to control the length of the additional resistance access time in the rotor circuit of the winding motor with the PWM method of the fixed carrier frequency so as to adjust the amplitude of the rotor current. The control slip is within about 10% of the range. This structure relies on the current reference value and current measurement value given by the external controller to calculate the resistance value of the rotor circuit. The resistance value of the rotor circuit is adjusted by turning on and off the power electronic device. The structure of such a power electronic device is relatively simple, but its stator side power factor is relatively low, and can only operate above the synchronous speed of the generator, and is a limited variable speed constant frequency system.
3 hybrid structure In order to reduce the cost of converter and can realize the wide-speed range operation of wind power generation system, a multi-variable converter topology based on double-fed motor chopper compensation and AC excitation control strategy was proposed. The chopper and inverter are combined together. The ingenious part of this structure is that the chopper and the inverter share a set of controllable power electronic switches, but due to the introduction of four contactor type controlled switches, The main circuit structure leading to this structure is complex, it is difficult to realize the transition of the synchronous speed switching process, and it is difficult to improve the power factor of the generator under the condition of higher than the synchronous speed operation.
To sum up, no matter which structure is used, it is very important to accurately evaluate and test the efficiency and performance of the frequency conversion system during the R&D process. Likewise, the overall monitoring of wind farms also requires precise testing.
The test points of wind power generators must be sharpened by their tools. Wind power generation from the R&D of motors to monitoring of wind farms requires a complete set of high-performance test instruments to achieve precise modulation and close monitoring.
1 Using power meters to accurately evaluate the performance of the frequency conversion system The wind power system frequency conversion system has a high modulation frequency bandwidth, a complex modulation method, and the object of modulation is also not a sinusoidal waveform. The waveform distortion is serious and contains a large number of frequency conversion components. Broadband power measurement and harmonic analysis capabilities. For this purpose, a power meter with stable performance and high accuracy needs to be selected as an auxiliary work. Take Yokogawa's WT3000 power meter as an example to briefly talk about testing in the wind power industry. The WT3000 can perform the latest IEC61000-4-7 harmonic analysis, the latest version of the IEC61000-4-7 harmonic measurement and voltage fluctuation/flicker measurement, bandwidth 0.1Hz ~ 1MHz, sampling rate 200kSa / s, ADC 16-bit, Power accuracy is 0.02%, with 4 input modules, 8.4-inch LCD display, and USB and Ethernet interfaces.
â— The relationship between the distorted waveform distortion and harmonics after frequency conversion is shown in Figure 1.
Figure 1. Relationship between waveform distortion and harmonics Distortion waveform measurement requires sufficient bandwidth. The distortion waveform contains high frequency components. The bandwidth of the measurement instrument is prone to error if it does not extend to a high frequency band. as shown in picture 2.
Figure 2 The bandwidth of the measurement instrument for different waveforms The WT3000 power meter can simultaneously perform power measurement and harmonic analysis of the frequency conversion system. The scheme is shown in Figure 3.
Figure 3 Measurement scheme based on the WT3000 power meter
â— Harmonic measurement method of frequency conversion system (as shown in Figure 4) 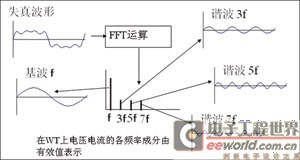
Fig. 4 harmonic measurement method of frequency conversion system Using the FFT operation function to convert the waveform from the time domain to the frequency domain, the method of measuring the frequency components to extract the superimposed signal frequency is as follows.
Fourier series: All periodic functions can be expressed by the sum of trigonometric functions.
Fourier integration: Set the period to infinity so that it applies to all functions.
Fourier transform: After the Fourier integral operation of the waveform's time function x(t), the frequency function X(f) can be obtained.
2 Using the oscilloscope to analyze the waveform signal in the inverter circuit in detail After PWM modulation, the power meter can obtain its electrical characteristics index, which provides an accurate reference for the R&D and inspection departments. If you want to further analyze the modulated waveform signal in detail, you need to use an oscilloscope with a CycleStatistics function (hereafter, Yokogawa DLM2000 series oscilloscope). The DLM2000's CycleStatistics function can effectively analyze periodically changing parameters when the fixed frequency/Duty ratio changes, or when the duty ratio/fixed/frequency changes, as shown in Figure 5.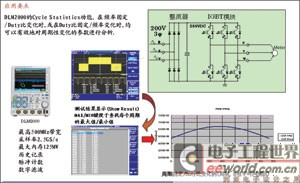
Figure 5 Using the DLM2000 Oscilloscope to Perform a Detailed Analysis of the Waveform Signals in the Variable Frequency Circuit 3 The overall monitoring of wind farm After the installation of wind power system, in order to ensure the stable operation of the wind turbine, the following signals must be monitored and recorded for a long time. These data are finally integrated into the monitoring center and stored for a long time.
â— Deformation of the blade.
â— Generator torque, speed, vibration and inrush current.
â— Atmospheric environment, such as: temperature, humidity, wind, wind speed, atmospheric pressure and other parameters.
â— Electric power parameters, such as: voltage, current, power, power parameters, frequency, etc.
Wind farm monitoring has several features: 1 The monitoring signals are complex and diverse; 2 The monitoring environment is harsh: At present, the domestic wind farms are mainly distributed in the northeast, Inner Mongolia, and Xinjiang, where the winter temperatures are very low, and the measurement instruments are presented high. The requirements; 3 each wind farm, there are a large number of fans, a large amount of monitoring data, wiring complexity.
Therefore, the monitoring of wind farms requires a variety of test equipment supporting work, but also have certain performance advantages to adapt to the special environment of wind farms. Take Yokogawa Electric's products as an example to explain the complete scheme of wind farm monitoring. As shown in Figure 6.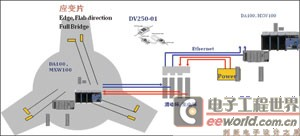
Figure 6 Complete plan for monitoring wind farms Firstly, the direct collection of the fan blade monitoring signal can be achieved through a slip ring (collector ring). The fan blade rotates continuously, which has a great influence on the installation and signal collection of the measuring instrument. Through the collector ring, the fan blade can be rotated. The signal line can stay still.
Then, using the data collector (MW100) for on-site data acquisition, monitoring, recording and transmission. The ambient temperature of the MW100 is -40°C to 70°C and it has a strong on-site adaptability. It can store data in the CF card, and the instant network is interrupted, and the collected data can also be well preserved. PR300 can also be used to achieve relatively inexpensive high-precision power parameter measurement and transmission. Accurately measure the generator's inrush current through the power meter WT3000. Finally, you can use the DAQWORX professional acquisition software to integrate display and record all data.
In summary, the field of wind power generation faces unprecedented opportunities for development. The development of its equipment systems, performance evaluation, and electric field monitoring are all moving toward increasingly sophisticated and increasingly complex directions. In order to meet such opportunities and challenges, the wind power industry has also put forward higher requirements for testing instruments at the tool level. Yokogawa’s global test solution providers are also actively responding. We believe that efficient and convenient testing products and solutions will provide strong support to the entire wind power industry.
Wind Energy Overview Compared with other types of new energy sources, the unique advantages of wind energy make it attractive for new energy development and utilization.
First, the reserves are large and widely distributed. China's proved theoretical wind energy reserves are 32.26×109 kW, while 2.53×109 kW can be exploited and utilized, and 7.5×109 kW of wind energy can be used offshore. The southeast coast of China and Inner Mongolia, Xinjiang, Gansu and other northeast and northwest regions are the largest areas of wind energy resources.
Second, the availability is strong and the cost is relatively low. At present, the cost of wind farms is about 8500 to 9,000 yuan/kWh, with units (equipment) accounting for about 70%, infrastructure 25%, and others 5%. Wind farm operation and maintenance costs are very low (about 3% to 5% of wind turbine components), and the construction period is short (about half a year). Once built, wind farms are an endless source of money.
Wind power technology core wind power system as a core part of the wind power generation field, technological progress is also changing. At present, there are two major categories of constant-speed constant-frequency wind generator systems and variable-speed constant-frequency wind generator systems.
Constant-speed constant-frequency wind power generation systems generally use synchronous motors or squirrel-cage asynchronous motors, and the rotational speed of the generator is maintained at a constant value through a wind turbine with a fixed pitch stall to ensure the frequency and amplitude of the generator-side output voltage. It is constant, its operating range is relatively narrow, and it can only capture wind energy at a certain wind speed, and its power generation efficiency is low.
Variable-speed constant-frequency wind power systems generally use permanent-magnet synchronous motors or doubly-fed motors as generators. By pitch-controlling the wind turbines, the entire system can be operated with the highest efficiency in a wide range of speeds. This is the current wind power technology. The direction of development. For wind turbines, the speed range is generally between 50% and 150% of the synchronous speed. If an ordinary squirrel cage induction motor system or a permanent magnet synchronous motor system is used, the capacity requirements of the inverter and the capacity of the generator being dragged Quite, very uneconomical. The stator of a doubly-fed asynchronous wind power generation system is directly connected to the power grid. The rotor and the power converter are connected. The power passing through the converter is only the differential power. This is a relatively high efficiency in various transmission systems. The structure is suitable for speed regulation. A wide range of wind power systems, especially large and medium-sized wind power systems.
The use of a wound induction motor as a generator and control of its rotor current is one of the main forms of realization of a variable-speed constant-frequency asynchronous wind power generation system. The main topology includes AC excitation control, rotor chopping resistance, and a hybrid structure developed from the combination of the two topologies.
1 AC excitation structure Excitation control The frequency converter provides three-phase slip frequency current to the rotor for excitation. Frequency converters in this method usually use cross-converters, matrix converters, or AC-DC converters.
2 The basic idea of ​​this structure is to use a controllable power electronic switch to control the length of the additional resistance access time in the rotor circuit of the winding motor with the PWM method of the fixed carrier frequency so as to adjust the amplitude of the rotor current. The control slip is within about 10% of the range. This structure relies on the current reference value and current measurement value given by the external controller to calculate the resistance value of the rotor circuit. The resistance value of the rotor circuit is adjusted by turning on and off the power electronic device. The structure of such a power electronic device is relatively simple, but its stator side power factor is relatively low, and can only operate above the synchronous speed of the generator, and is a limited variable speed constant frequency system.
3 hybrid structure In order to reduce the cost of converter and can realize the wide-speed range operation of wind power generation system, a multi-variable converter topology based on double-fed motor chopper compensation and AC excitation control strategy was proposed. The chopper and inverter are combined together. The ingenious part of this structure is that the chopper and the inverter share a set of controllable power electronic switches, but due to the introduction of four contactor type controlled switches, The main circuit structure leading to this structure is complex, it is difficult to realize the transition of the synchronous speed switching process, and it is difficult to improve the power factor of the generator under the condition of higher than the synchronous speed operation.
To sum up, no matter which structure is used, it is very important to accurately evaluate and test the efficiency and performance of the frequency conversion system during the R&D process. Likewise, the overall monitoring of wind farms also requires precise testing.
The test points of wind power generators must be sharpened by their tools. Wind power generation from the R&D of motors to monitoring of wind farms requires a complete set of high-performance test instruments to achieve precise modulation and close monitoring.
1 Using power meters to accurately evaluate the performance of the frequency conversion system The wind power system frequency conversion system has a high modulation frequency bandwidth, a complex modulation method, and the object of modulation is also not a sinusoidal waveform. The waveform distortion is serious and contains a large number of frequency conversion components. Broadband power measurement and harmonic analysis capabilities. For this purpose, a power meter with stable performance and high accuracy needs to be selected as an auxiliary work. Take Yokogawa's WT3000 power meter as an example to briefly talk about testing in the wind power industry. The WT3000 can perform the latest IEC61000-4-7 harmonic analysis, the latest version of the IEC61000-4-7 harmonic measurement and voltage fluctuation/flicker measurement, bandwidth 0.1Hz ~ 1MHz, sampling rate 200kSa / s, ADC 16-bit, Power accuracy is 0.02%, with 4 input modules, 8.4-inch LCD display, and USB and Ethernet interfaces.
â— The relationship between the distorted waveform distortion and harmonics after frequency conversion is shown in Figure 1.

Figure 1. Relationship between waveform distortion and harmonics Distortion waveform measurement requires sufficient bandwidth. The distortion waveform contains high frequency components. The bandwidth of the measurement instrument is prone to error if it does not extend to a high frequency band. as shown in picture 2.
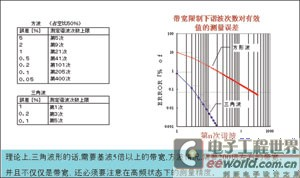
Figure 3 Measurement scheme based on the WT3000 power meter
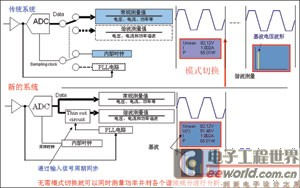
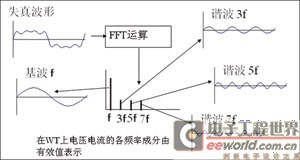
Fig. 4 harmonic measurement method of frequency conversion system
Fourier series: All periodic functions can be expressed by the sum of trigonometric functions.
Fourier integration: Set the period to infinity so that it applies to all functions.
Fourier transform: After the Fourier integral operation of the waveform's time function x(t), the frequency function X(f) can be obtained.
2 Using the oscilloscope to analyze the waveform signal in the inverter circuit in detail After PWM modulation, the power meter can obtain its electrical characteristics index, which provides an accurate reference for the R&D and inspection departments. If you want to further analyze the modulated waveform signal in detail, you need to use an oscilloscope with a CycleStatistics function (hereafter, Yokogawa DLM2000 series oscilloscope). The DLM2000's CycleStatistics function can effectively analyze periodically changing parameters when the fixed frequency/Duty ratio changes, or when the duty ratio/fixed/frequency changes, as shown in Figure 5.
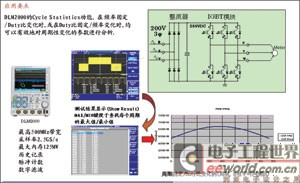
Figure 5 Using the DLM2000 Oscilloscope to Perform a Detailed Analysis of the Waveform Signals in the Variable Frequency Circuit
â— Deformation of the blade.
â— Generator torque, speed, vibration and inrush current.
â— Atmospheric environment, such as: temperature, humidity, wind, wind speed, atmospheric pressure and other parameters.
â— Electric power parameters, such as: voltage, current, power, power parameters, frequency, etc.
Wind farm monitoring has several features: 1 The monitoring signals are complex and diverse; 2 The monitoring environment is harsh: At present, the domestic wind farms are mainly distributed in the northeast, Inner Mongolia, and Xinjiang, where the winter temperatures are very low, and the measurement instruments are presented high. The requirements; 3 each wind farm, there are a large number of fans, a large amount of monitoring data, wiring complexity.
Therefore, the monitoring of wind farms requires a variety of test equipment supporting work, but also have certain performance advantages to adapt to the special environment of wind farms. Take Yokogawa Electric's products as an example to explain the complete scheme of wind farm monitoring. As shown in Figure 6.
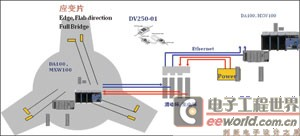
Figure 6 Complete plan for monitoring wind farms
Then, using the data collector (MW100) for on-site data acquisition, monitoring, recording and transmission. The ambient temperature of the MW100 is -40°C to 70°C and it has a strong on-site adaptability. It can store data in the CF card, and the instant network is interrupted, and the collected data can also be well preserved. PR300 can also be used to achieve relatively inexpensive high-precision power parameter measurement and transmission. Accurately measure the generator's inrush current through the power meter WT3000. Finally, you can use the DAQWORX professional acquisition software to integrate display and record all data.
In summary, the field of wind power generation faces unprecedented opportunities for development. The development of its equipment systems, performance evaluation, and electric field monitoring are all moving toward increasingly sophisticated and increasingly complex directions. In order to meet such opportunities and challenges, the wind power industry has also put forward higher requirements for testing instruments at the tool level. Yokogawa’s global test solution providers are also actively responding. We believe that efficient and convenient testing products and solutions will provide strong support to the entire wind power industry.
Silica Sand,Silica Sand For Glass,Quartz Silica Sand
Filter Media,Activated Carbon Co., Ltd. , http://www.zjactivatedcarbon.com