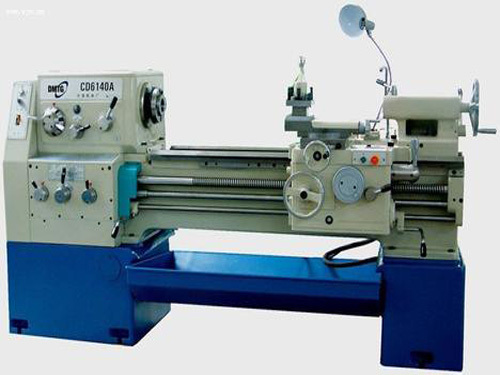
The significance of green machine tool design As a pillar industry of the national economy, manufacturing has created rich material wealth for society, but it consumes a lot of resources and causes environmental pollution. At present, environmental issues have increasingly become a key factor affecting socio-economic development. The environmental protection laws and regulations formulated by various governments have become more and more stringent, and consumers have also paid great attention to environmental management. Therefore, how to reduce resource consumption and environmental pollution is a major issue facing the manufacturing industry in the 21st century. For this reason, implementing green manufacturing technologies in the manufacturing industry and implementing the strategy of sustainable development are imperative. Machinery manufacturing plays an important role in China's energy-saving and emission reduction work. Metal-cutting machine tools are machine-building machines and are industrial master machines. The working life of general machine tools is more than 30 or 40 years. It belongs to long-life products. In the life cycle, it is necessary to consume energy, but also produce solid, liquid and gas wastes, causing direct or indirect pollution to the work environment and the natural environment [1]. Therefore, new types of machine tools that save energy and protect the environment have become the focus of current research.
New materials for green machine design With the continuous improvement of modern engineering technology and science and technology requirements for material properties, the research and application of new materials have been rapidly developed. New materials represented by composite materials have been widely used in various fields of the national economy. In the machinery industry, the emergence and application of new materials has led to major changes in some traditional processing technologies. The development of high-tech industries such as modern aerospace industry has increasingly increased the requirements for the performance, precision, and processing capabilities of CNC machine tools and equipment, and has driven and promoted the development of CNC machine tools and equipment manufacturing.
Due to the characteristics of high-temperature, high-strength, difficult-to-process, high-alloy and composite materials, and many complex structural parts and high process requirements, parts for aerospace industrial products require large-scale (heavy-duty, super-heavy), high-speed, precision machining equipment. Compound and intelligent trend development. How to give full play to the advantages of new materials, such as process performance, apply it to practice, and become an important issue in the field of machine tool design in the new era.
The application of new materials including carbon fiber, ceramics and composite materials in the machine tool structure has made the machine tool structure lightweight and environmentally friendly, and has promoted the development of high-speed, precision, compound and intelligent machine tool processing equipment. Such as the use of artificial granite granite large-scale support, or in the framework of welded steel plate filled with concrete, not only can save metal resources, but also can increase the vibration resistance and thermal stability; For some stress conditions, complex parts and components Using new materials such as carbon fiber can not only make the machine tool structure lightweight, but also can increase the life; For some high hardness wear parts, the use of ceramics and other materials instead of high hardness steel, can reduce weight, but also can save precious metals Resources can also eliminate time-consuming energy-consuming heat treatment processes that are required for high-hardness steels to be processed many times during processing.
For example, in the machine tool industry in countries such as Europe and America, new material resin concrete has been greatly developed, especially in the bed application of high-precision machine tools, resin concrete is gradually replacing the traditional cast iron. Resin concrete is an emerging structural material, a mixture of natural ore (different sizes, different sources) and epoxy resins (as binders), which has a great advantage over traditional cast iron. At present, more and more international machine tool manufacturers begin to design resin concrete machine tools, but for the Chinese market, this area is still blank. Compared with traditional cast iron, resin concrete has the following four advantages:
(1) Low energy consumption. Compared to cast iron, resin concrete consumes less energy and saves about 30% of energy consumption during the manufacturing process. In the face of energy shortages such as electricity, natural gas, and coal, the use of eco-friendly materials such as resin concrete, which is inexpensive and can be recycled, is the best choice. Resin concrete waste and old beds can be used as building materials.
(2) Good vibration absorption. Nowadays, more and more attention is paid to precision CNC machine tools. In high-speed cutting, workpieces and machine parts move faster and faster. Increasing the speed, feed rate, and increasing the weight of the parts will generate vibrations that reduce accuracy. Resin concrete eliminates vibration and improves the accuracy of the machine.
(3) Highly integrated. Casting temperature of ±45°C for resin coagulation is another advantage compared to cast iron at 900°C casting temperature. The traditional method is to install other components after the bed has been cast. It is now possible to cast components such as pipes, cables, sensors, actuators, and fluid-filled chambers directly into the casting.
(4) High precision. The traditional method of manufacturing the bed is to install linear guides after milling and grinding. Because the precision of traditional castings after demoulding is low, resin concrete after demoulding can achieve higher precision. In addition, higher levels of precision can also be achieved by recasting.
The new technology of green machine design With the rapid development of science and technology, more and more new technologies are applied to the design of machine tool products. The green machine tool proposes a brand-new idea: to reduce the quality of the machine tool, save material, and reduce the energy consumption when the machine tool is used. At the same time, modular design is gradually adopted in the design of machine tools to meet the needs of different users, and it is easy to repair, disassemble and recycle the products, so that resources are used to the maximum extent and resources are saved.
1Reducing weight, simplifying structure, and optimizing functions in structural design When designing machine tools, most of them adopt analogy design method and change or improve on the basis of the original product. If the original product does not have problems, some structures and sizes will be copied. Come here, or scale it up. This will produce a surplus of structural dimensions. Therefore, the space for optimization of the machine tool structure is very large. In the life cycle of the machine tool for several decades, the energy saving amount is considerable.
When designing the overall structure of the machine tool, the principle of the simplest structure is adopted, and the design is simplified as much as possible to reduce the number of unnecessary parts. Because behind each part, there is a complete set of design process, from the preparation of blanks to the production process after the product inspection pass, all the management processes, and the adjustment process at the time of installation. Reducing one part reduces the entire process and reduces manufacturing costs. When designing the drive system of the machine tool, shorten the transmission chain as much as possible, not only can reduce the number of parts, reduce no-load power loss, but also can improve the transmission accuracy. In the part design process, the principle of the simplest structure is also adopted. After the basic part design of the machine tool is completed, the finite element structure analysis is performed. Under the premise of satisfying the rigidity, optimization is improved, certain dimensions are reduced, the weight of the machine tool is minimized, and material is saved. Fig. 1 shows a large-scale finite element analysis of a machine tool. For some moving parts, structural optimization design can save materials, but also reduce the weight, reduce the idle power and the energy consumption when the machine is in use.
In the case of the large aircraft project of China's aviation and aerospace industry, the plates or forgings used for the beams, frames, ribs and sidings of large aircraft are all weighing several hundred kilograms or even several tons, and therefore require heavy or even super-heavy. Multi-coordinate, high-speed, high-rigidity, high-power CNC milling machine, vertical machining center and other CNC machining equipment. Simplifying the structure, optimizing functions, and reducing weight during the design of the machine tool can save a large amount of materials and achieve good social and economic benefits.
2 Adopting new environmental protection technologies to effectively use energy and protect the ecological environment During the process of designing new machine tools, emphasis is placed on the effective use of resources and energy and the protection of the ecological environment, minimizing the consumption of non-renewable resources and saving raw materials. In practice, it mainly controls noise pollution, exhaust pollution, cutting fluid contamination, lubricant contamination, and the use of hazardous substances. In response to the above requirements, there are many new environmental protection technologies applied to the design of machine tools.
For example, lubricating coolants during the use of machine tools are harmful emissions, especially the emulsions used in grinding are very harmful to the environment and workers' health. Now, dry cutting and Minimalized Lubrication (MQL) technology has emerged. Improve the performance of the tool, do not use coolant, or use a special device to provide aerosol or low-temperature air (cold) to solve the problem of cutting fluid contamination. Figure 2 is a schematic of a trace amount lubrication technique.
At the same time, in the design of the lubrication system of the machine tool, centralized lubrication or self-lubrication can effectively reduce the loss and discharge of lubricating oil and reduce the environmental pollution of lubricating oil. In the modern aerospace industry, magnesium alloys are widely used due to their low density and high specific strength, which can achieve weight reduction. On aircraft, magnesium alloys are used to make wall plates, ribs, wheel hubs, and motor housings. In the aerospace industry, magnesium alloys are used to make rockets, satellites, and many other components. Magnesium alloy powder is prone to hydrogen generation when it encounters water, and hydrogen is easy to burn. It is explosive. Therefore, magnesium alloys can not be flushed with high feed rates and high-speed cutting, and only mineral oil can be used, which has a high cost. Magnesium alloy has the characteristics of no need of grinding and polishing, fast heat dissipation, and good surface quality without using cutting fluid. Therefore, the appearance of dry cutting and trace amount lubrication and other environmental protection technologies solve the problem of magnesium alloy material processing in the aerospace industry. Reduced processing costs.
Modular design facilitates reorganization and green remanufacturing. In the design of new machine tools, the modular design can meet the needs of different users. It is easy to repair, disassemble and recycle the product, so that resources are used to the maximum extent and resources are saved. Combination machines are a good example of modular design and ease of recycling. The combined machine tool is a highly efficient dedicated machine tool consisting of a large number of universal parts and a small number of special parts. When the product or process changes, the original machine tool is disassembled, and a large number of universal parts can also be reused to the new machine tool. On the basis of existing standards, if certain standards can be established for the size of major parts of general-purpose machine tools, it will be beneficial to the recovery, modification or reorganization of machine tools, which will greatly save machine tools and cause this [2]. Figures 3 and 4 show the modular design of the turning products and the boring and milling products, respectively.
Conclusion With the deepening of research on new materials and new technologies, the continuous development of new machine tools that save energy and green ecology has been greatly promoted. China is a big manufacturing country, improving the ability of independent innovation in the industry, applying new materials and new technologies to develop green machine tools, realizing the recycling of resources, realizing the overall optimization of the economic and social benefits of enterprises, and has important strategic significance for the revitalization of China's machine tool industry. Social energy saving and emission reduction has a significant role in promoting.
Mini Type Fiber Laser Marking Machine
Fiber Laser Marking Machine Mini type, easy to carry, easy to operate. MiniMini Type Fiber Laser Marking Machine Type Fiber Laser Marking Machine
This fiber laser marking machine price is economic with best quality, and it mainly used for marking on metal and nonmetal material, it can marking on mobile phones buttons, plastic translucent keys, electronic components, integrated circuits(IC), electrical appliances, communication products,sanity ware,tools, accessories,knifes,medical device industry,jewelry, glass and clocks,auto parts,luggage buckle,cooking utensils,stainless steel products and other industries, etc.
Why fiber laser marking machine is better
1. Producing higher quality beam,higher photoelectric conversion, the marking quality will be more finer and higher precision.
2. Small Size wtih Air cooling,no water chiller.
3. No maintenances laser source(100,000 hours service time), Easy to adjust focus, low operation cost (LOw power consumption) Maintenance free without routine replacement of consumables Easy to use by unskilled operator
4. Old lamp and diode pump laser marking machine, both need maintenance the laser source(replace lamp or diode laser modular every year), also require an water chiller to control heat
fiber laser marking machine, laser marking machine, mini type fiber laser
Jinan Transon Cnc Equipment Co., Ltd. , https://www.csjiguang.com