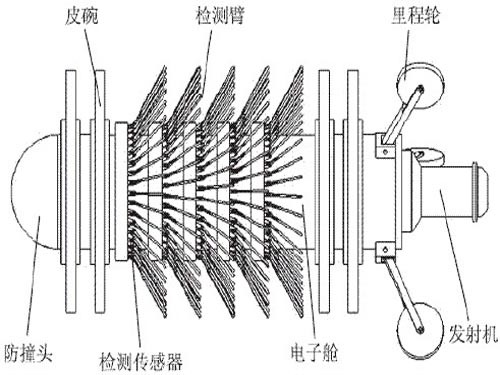
It was learned from the China National Petroleum Pipeline Bureau that a 1219 mm diameter HD flux leakage detector was successfully removed from the collection cylinder of the Lingtai Compression Station of the Second West-East Gas Pipeline, indicating that China's pipeline magnetic flux leakage detection technology has entered the three-axis era.
Magnetic flux leakage testing is a non-destructive testing method, which has been widely used due to reliable detection results and small influence of human factors. The principle is that a magnetic flux leakage detector is placed in the pipeline, and the wall of the pipeline is magnetized by the magnet carried by the detector itself. By detecting the change of magnetic lines, defects in the pipeline are found.
The magnetic flux leakage detector for industrial applications is a three-axis testing device developed by the Pipeline Inspection Company over three years and has fully independent intellectual property rights. It is currently the largest domestic pipeline inspection device with the highest degree of technological integration. Compared with the single-axis detection, the three-axis detection technology has the functions of radial, axial and circumferential defect recognition in three directions. It has the advantages of high detection accuracy, strong ability to identify corrosion defects, etc., and can realize the full range of in-service pipelines. Testing.
The detector adopts ceramic probe wear-resistant scribes, which completely changes the technical problem that the detector probe has insufficient abrasion resistance. The speed control system meets the high-pressure and large-flow industrial pipeline inspection process requirements, and realizes high-pressure pipelines without declining the amount of in-service testing, providing a reliable guarantee for accurate data collection. Once the speed control system fails, the self-locking device will automatically start, enabling the detector to smoothly enter the ball collection barrel. The successful application of these technologies has filled the domestic gap.
After the completion of this test, the data is clear and complete, the speed control system is working properly, and the triaxial ceramic probe is intact, indicating that the technology of this product is mature and stable. This will further accelerate the serialization process of the three-axis HD flux leakage detector and better The top foreign inspection companies competed on the same platform to provide technical support.
It is reported that in 2013, Pipeline Inspection Company successively developed the first three-axis high-definition magnetic flux leakage detectors with diameters of 711 mm and 1016 mm in China, and successfully applied them to the experimental sections of Southwest Oil and Gas Field and West-East Gas Pipeline.
Disclaimer: This article only represents the personal opinion of the author and has nothing to do with this site. This article is posted on this site for the purpose of passing more information and does not imply endorsement of its views or confirmation of its description. The content of the article is for reference only, please check the relevant content
Pulse Valve Repair Diaphragm, Pulse Valve Guide Tube, Pulse Valve Replacement Repair Kits
NINGBO BRANDO HARDWARE CO.,LTD , http://www.brandopneumatic.com