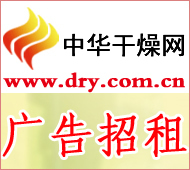
China's existing coke oven production capacity is relatively large, accounting for the world's first, coking coal water is high, and high-quality coking coal is increasingly in short supply, around the existing coke oven and coking production process, develop a new process to improve the quality of coke and the use of coke waste heat The new technology is an effective way to adapt to the development of enterprises and improve the economic efficiency of enterprises. The coal moisture control technology can reduce the moisture of the coal entering the furnace, reduce the coke-consuming heat, increase the density of coal into the furnace, and improve the quality of coke. Among them, drying equipment is the most important pipe fitting.
Roller drying equipment
The heat medium used for drying coal is prepared in a hot blast stove. The air sent by the blower through the air duct and the gas sent from the gas pipe is combusted by the burner and burned to generate hot flue gas to the energy-saving drum dryer to heat the wet coal. The cake absorbs moisture and evaporates. The waste gas enters the cyclone dust collector arranged side by side through the discharge box and the air duct to recover the coal powder. The gas after preliminary purification is sent to the wet dust collector for further purification by the induced draft fan through the air duct. The clean exhaust gas is discharged into the atmosphere from the exhaust chimney. The fine pulverized coal collected by the primary cyclone dust collector is sent to the discharge scraper conveyor through the screw conveyor and the star discharge valve and mixed into the dried product and returned to the original conveying system. The black water discharged from the second-stage wet dust remover is recycled into the original trench and returned to the coal processing plant for centralized treatment. The coal moisture control system adopts intelligent control and monitoring, and has strong production adaptability. The product can fully meet the requirements of users.
Energy-saving drum dryer is the earliest application, and it is a kind of drying equipment with a relatively large number of current operations, and the work is reliable. According to the characteristics of the materials, the internal and external structures of the cylinder were further improved and an energy-saving drum dryer was developed. The characteristics are: the heat loss of the external surface of the cylinder is reduced; and the problem of sticking material on the internal wall of the cylinder is reduced or eliminated. There is no ash increase in the product; the smoke heat loss is further reduced and the dry heat efficiency reaches 80%. Improve the design of the guide device, so that fine particles, large moisture, high viscosity material can be smoothly diverted into the drum, running more secure and reliable.
In recent years, the coal-moisturizing technology has emerged in the coking industry at home and abroad and has been widely used. The reason is that the coal moisture-conditioning technology has its unique advantages: it can increase the production of coke and chemical products by 11%, and increase economic efficiency; The heating of the coke oven is reduced by the use of fuel, which reduces the consumption of heat; the quality of the coke is improved; the coke oven waste heat is fully utilized, and obvious economic and social benefits are achieved.
News link:
The coal moisture control workshop comes from the belt conveyor, and the pear unloader is intercepted by the tape transporter and fed into the sealed scraper conveyor through the chute. It enters the dryer through the chute, and the heat exchange process is completed in the dryer. The discharge box is discharged into the sealed discharge conveyor, sent into the belt conveyor through the chute, and then transferred through two belt conveyors to return to the original conveyor system.
The heat medium used for drying coal is prepared in a hot blast stove. The air sent by the blower through the air duct and the gas sent from the gas pipe is combusted by the burner and burned to generate hot flue gas to the energy-saving drum dryer to heat the wet coal. The cake absorbs moisture and evaporates. The waste gas enters the cyclone dust collector arranged side by side through the discharge box and the air duct to recover the coal powder. The gas after preliminary purification is sent to the wet dust collector for further purification by the induced draft fan through the air duct. The clean exhaust gas is discharged into the atmosphere from the exhaust chimney. The fine pulverized coal collected by the primary cyclone dust collector is sent to the discharge scraper conveyor through the screw conveyor and the star discharge valve and mixed into the dried product and returned to the original conveying system. The black water discharged from the second-stage wet dust remover is recycled into the original trench and returned to the coal processing plant for centralized treatment. The coal moisture control system adopts intelligent control and monitoring, and has strong production adaptability. The product can fully meet the requirements of users.
Electric Scooter Battery Pack is the heart of Electric Scooter;
A little bit different with traditional packing work, the scooter battery pack
has much more tech requirements for the IC parts and connection.
The basic quality standard of Electric Scooter Battery pack deeply rooted in the
18650 Lithium Battery cells and IC.
Electric Scooter Battery Pack
Electric Scooter Battery Pack,Electric Scooter Lithium Battery,Electric Bike Battery,Harley Electric Scooter Battery Pack
Shenzhen Mkarda Technology Co.,Ltd , http://www.mkarda.com