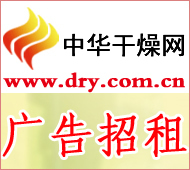
“As the largest chlor-alkali province, Shandong's chlor-alkali production capacity has accounted for more than a quarter of the country's total production capacity. To solve the problem of overcapacity for enterprises, we invited experts and representatives to work together on new product development and new technologies for the chlor-alkali industry. The application of new technologies and optimization of the chlor-alkali industry chain will be further discussed in an effort to make the chlor-alkali enterprises in Shandong gradually out of the predicament.†On June 21st, at the 4th meeting of the Shandong Province Chlor-Alkali Industry Association held in Qingdao, the chlor-alkali industry association of Shandong Province Director Jiang Zhenghui told reporters.
According to Wei Xiaoyu, an engineer at Dezhou Shihua Chemical Co., Ltd., in order to solve the long-term high cost and pollution problems of vinyl chloride series products, they jointly developed with the Shanghai Institute of Advanced Research, Ke Yigong (Xiamen) Chemical Technology Co., Ltd. of the Chinese Academy of Sciences. A new process for the synthesis of vinyl chloride was designed and a 100-ton pilot plant was designed. On April 8th this year, the 100-ton test for the acetylene and dichloroethane catalytic reforming of vinyl chloride projects was successful and passed expert appraisal. The new process is evaluated by the experts as an international advanced level with its simple process, low energy consumption, low equipment investment, small footprint, low production cost, no pollution, and high process feasibility.
At present, Texas Shihua is building a full-process production line with an annual capacity of 2,000 to 5,000 tons, which is expected to be put into operation by the end of July. The reactor specification, production process, and instrumentation control in the production line have reached the annual production capacity of 200,000 tons of vinyl chloride, and they plan to start construction of two 200,000-ton-per-year vinyl chloride scales in the Shihua New Park in Dezhou in 2014. The production line will realize the first mercury-free PVC industrialized production line and will be promoted nationwide.
As a domestic developer of high-performance perfluorosulfonic acid ion membranes, Shandong Dongyue Group has ordered a new machine head capable of producing 1.5-meter-wide ion membranes and set up a corresponding research team. “Now we are developing the latest generation of slotted fiber membranes with sacrificial fibers, which are more suitable for high-density zero-polarity channels. The new membranes will be close to the mainstream foreign companies' membranes,†said the Dongyue Group’s technical staff.
Yang Xiuling, general manager of Shandong Xinlong Technology Co., Ltd., told reporters: “In recent years, we have strengthened the research and development of new products and new technologies, upgraded the traditional chlor-alkali products, and eliminated the impurities in chlorine products to increase their purity. From industrial grade to electronic grade, food grade, now high-purity hydrogen, electronic grade hydrogen chloride, electronic grade hydrogen peroxide projects have been put on the market one after another.â€
It is understood that electronic grade hydrogen chloride is mainly used for the epitaxial production of polysilicon and semiconductors in photovoltaic companies. Due to quality reasons, the former domestic products mainly depended on imports. After the electronic grade hydrogen chloride products of Xinlong Chemical was launched, it was buoyed by the market and broke the monopoly of foreign companies in China.
Yang Xiuling believes that according to the state's newly-built, rebuilt, and expanded calcium carbide process polyvinyl chloride production projects, the requirements for low-mercury catalyst must be used. Chlor-alkali enterprises must not only produce chemical products, but also have a sense of social responsibility. “We are developing a dry acetylene plant with independent intellectual property rights, and we have developed a mother liquor recovery unit and a patented acetylene and chlorine drying technology that improves the use of low-mercury catalysts. This is achieved through the acquisition of Ningxia Jinhai Changke Chemical Company. The mercury catalyst production technology and patented enterprises have established a low-mercury catalyst research and development center to form a low-mercury catalyst professional technical service team with professional and technical personnel to participate in, and vigorously promote the promotion of environmentally friendly low-mercury catalysts, said Yang Xiuling.
The low mercury catalyst is not only safe and environmentally friendly, but also brings considerable economic benefits. Yang Xiuling calculated for us: The use of the same single converter catalyst is 566 kg less than that of the high mercury catalyst. Since the use volume is reduced by 10%, the cost per ton of PVC can be reduced by 24.58 yuan, and the annual output is 200,000 tons. PVC calculations can reduce costs by more than 4.9 million yuan per year for enterprises.
The reporter learned from Yangtong Hengtong Chemical Co., Ltd. that in order to realize the development goal of constructing billions of chemical cities, the company plans to use international advanced technology to invest in the reconstruction of annual output of 300,000 tons of PVC raw materials and to produce 200,000 tons of hydrogen peroxide per year. Propylene oxide cleaner production project. The project will be constructed in two phases. The first phase of the project will be an annual output of 300,000 tons of methanol-made olefin complete sets of equipment and an annual output of 300,000 tons of PVC raw material route transformation equipment and supporting public utilities and ancillary facilities; the second phase of the project is to produce 200,000 tons annually. Hydrogen peroxide-based propylene oxide cleaner production equipment and supporting utilities and ancillary facilities. After the first phase of the project is put into operation, annual sales income of 3353.7 million yuan, profit of 371 million yuan, and tax of 141.4 million yuan will be realized.
The new project was started on April 28 in Hengtong Chemical Park. Since the new technology selected in the new project has the advantages of low investment, low consumption of raw materials, high utilization of raw materials, low waste emission, and clean environmental protection, the project can save more than 100 years of fresh water compared with traditional process equipment after the project is implemented. 10,000 tons, 540,000 tons of calcium carbide slag (dry basis), 20% energy saving per ton of PVC, significant social and environmental benefits, in line with national industrial policies and environmental protection requirements.
It is not only Yangmei Hengtong that realizes the upgrade and transformation with new projects. In the petrochemical industrial base of Lingang Industrial Zone in Dongjiakou, Qingdao, the relocation project of Qingdao Haijing Chemical Co., Ltd. is proceeding in an orderly manner. They will achieve a complete upgrade of the enterprise during the relocation process. At present, the pouring of the outer tank of the low temperature ethylene plant of the entire project has been completed. Due to the connection with international top companies and technologies, the completed Haijing Chemical Project will be more advanced, safer and more environmentally friendly than existing facilities and processes.
Beer Fermenter Tank,Stainless Steel Fermentation Tank,Beer Fermentation Tank,Stainless Conical Fermenter
Stainless Steel Tank Co., Ltd. , http://www.worldinstruments.info